La stampa 3D in metallo è un argomento sempre più discusso. Secondo il Wohlers Report 2024, questo settore ha registrato una crescita del 24,4% nell’ultimo anno, superando l’incremento complessivo del mercato additivo, che si è attestato all’11,1%. Questo sviluppo è spinto dalla crescente domanda di applicazioni industriali e da tecnologie all’avanguardia, tra cui il processo Cold Metal Fusion (CMF).
Ti interessa la stampa 3D in metallo e vuoi sapere cos’è la tecnologia CMF? In questo articolo ti illustreremo come funziona, perché rappresenta una svolta tecnologica e in che modo si differenzia dagli altri processi di produzione dei metalli.
Cos’è la tecnologia Cold Metal Fusion?
Cold Metal Fusion, o CMF, è un metodo di fabbricazione indiretta dei metalli che unisce il processo di stampa 3D SLS, ampiamente utilizzato per la produzione di componenti in plastica, con il processo di debinding e sinterizzazione della metallurgia delle polveri. Questa tecnologia, sviluppata dall’azienda tedesca Headmade Materials, si propone di rendere la produzione di parti metalliche più efficiente e accessibile rispetto ai metodi tradizionali di stampa 3D per metalli.
Materiali innovativi
Il cuore della tecnologia CMF è costituito dal materiale di partenza, che consiste in polvere metallica integrata in una matrice di legante plastico.
Questa caratteristica consente di utilizzare sia polveri metalliche (come acciaio inossidabile 316L, Acciao 17/4, Acciaio M2 e Titanio Ti6Al4V) sia polveri polimeriche tradizionali (per esempio PA12, PA11, TPU o Polipropilene) con la stessa stampante 3D.
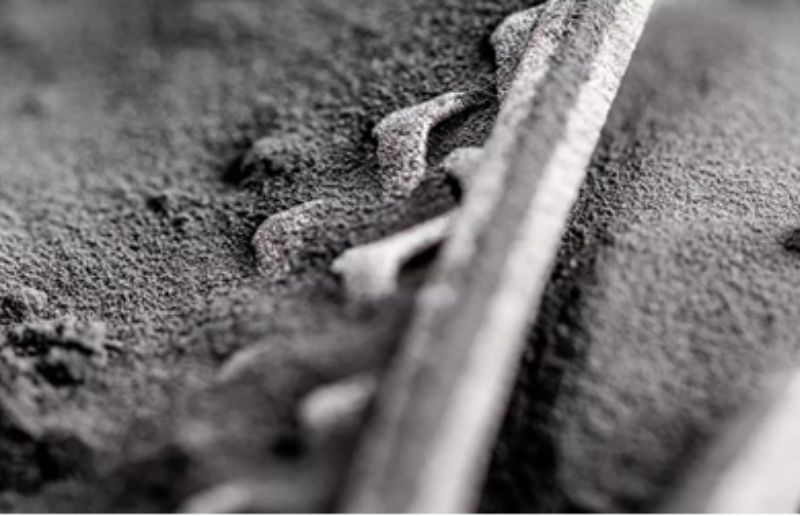
Come funziona il processo Cold Metal Fusion
Cold Metal Fusion si basa su tecnologie consolidate come la stampa 3D SLS, il debinding con solvente e la sinterizzazione. Ecco le principali fasi del processo:
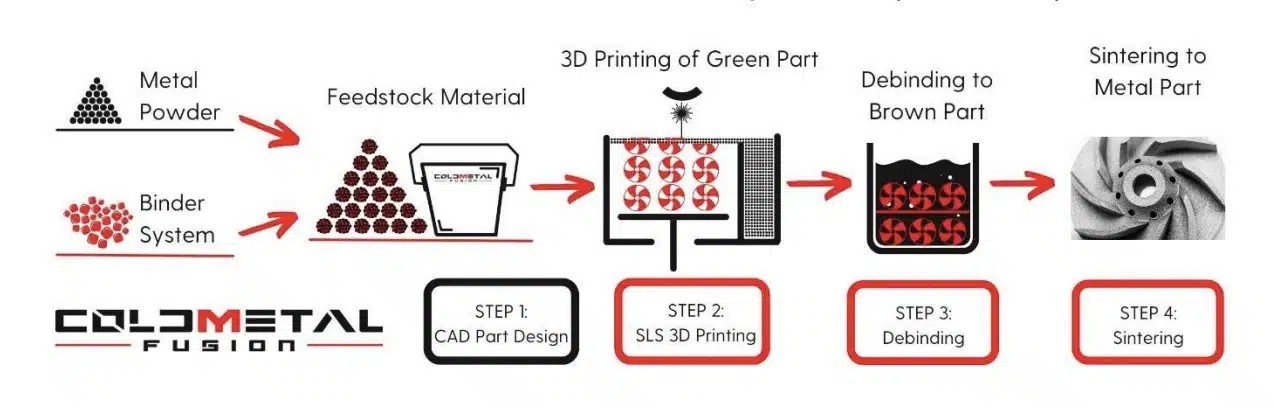
Fase 1: Progettazione CAD
Il processo inizia con la creazione di un modello 3D in un software CAD.
Utilizzando polvere metallica come materia prima, durante il processo di sinterizzazioni le parti si riducono in tutte le direzioni (XYZ) di circa il 14%, quindi la dimensione del file da stampare va riparametrata secondo formule specifiche. Dopo la progettazione, il modello viene inserito nel software della stampante dove viene preparato per la produzione.
Fase 2: Stampa SLS
Il pezzo viene creato strato per strato utilizzando un sistema di sinterizzazione laser per materie plastiche (SLS). Durante il processo, il materiale di partenza viene fuso, formando quello che viene definito un “pezzo verde”. Il legante plastico si fonde a una temperatura relativamente bassa, inferiore agli 80°C e spesso sono sufficienti solo 50°C (questo è il motivo per cui il processo viene chiamato “cold”, ossia freddo), riducendo notevolmente i tempi di riscaldamento e raffreddamento.
La stampa 3D SLS consente anche un processo chiamato “stacking”, che permette la sovrapposizione di più parti nello stesso ciclo produttivo.
Grazie alla protezione offerta dalle particelle polimeriche, le particelle di metallo non vengono esposte all’aria, prevenendo così l’ossidazione.
Fase 3: Rimozione della polvere
Una volta raffreddato il letto di polvere, il materiale non fuso viene rimosso e riutilizzato.
Il processo a freddo non ha alcun impatto termico sulla polvere non sinterizzata, il che ne consente il riutilizzo del 100% della polvere rimanente in future stampe.
Fase 4: Debinding con solvente
I pezzi vengono sottoposti a un trattamento con solvente per eliminare la parte polimerica. Questo processo avviene a una temperatura relativamente bassa, tra i 30 e i 40°C, e permette di ottenere la cosiddetta parte “marrone” del metallo. Il debinding con solvente è una tecnica consolidata e altamente efficiente dal punto di vista economico ed ecologico, già ampiamente utilizzata nella metallurgia delle polveri. I solventi, dopo l’uso, vengono distillati e riutilizzati più volte, creando un ciclo di produzione chiuso che minimizza l’impatto ambientale.
Fase 6: Sinterizzazione
Dopo il debinding, il pezzo passa alla fase di sinterizzazione, dove viene riscaldato lentamente fino alla temperatura necessaria per completare il processo. Durante questa fase, la piccola quantità di legante plastico ancora presente (circa l’1-3%) brucia senza lasciare residui. A temperatura di sinterizzazione, le particelle metalliche si fondono tra loro, creando una struttura solida e densa che conferisce al pezzo le proprietà finali di un componente metallico completo.
Fase 7: Finitura
Infine, il pezzo metallico sinterizzato può essere sottoposto a vari trattamenti di finitura, come lucidatura, sabbiatura o anodizzazione, a seconda delle esigenze.
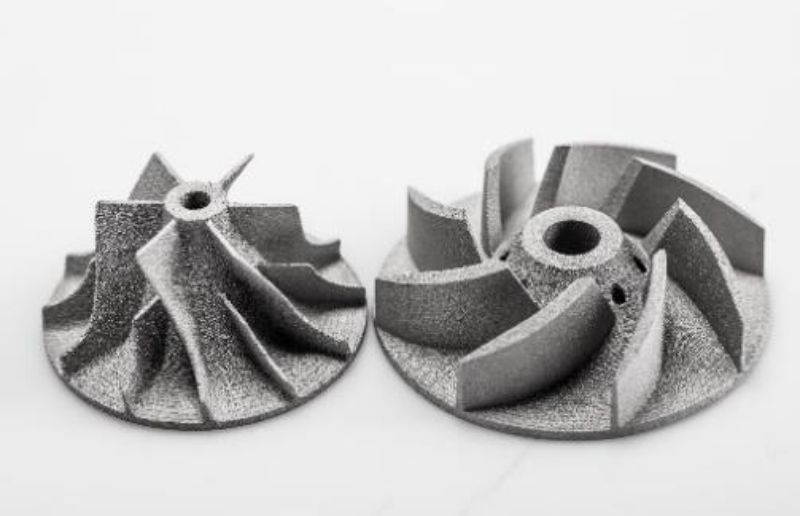
Differenze rispetto alle altre tecnologie
Cold Metal Fusion (CMF) si distingue dalle altre tecnologie di stampa 3D metallica, come la Powder Bed Fusion (PBF) e il Binder Jetting (BJT), per aspetti chiave legati al processo, ai materiali utilizzati e ai vantaggi produttivi.
Nella tecnologia PBF, il metallo viene fuso direttamente con un laser o un fascio di elettroni, ma richiede un consumo energetico elevato e presenta rischi di distorsione termica. Nonostante garantisca alta precisione e qualità superficiale, PBF è un processo costoso per il prezzo delle macchine (laser o fascio di elettroni), l’alto consumo energetico e la gestione manuale del Post Processing.
Nel processo di Binder Jetting (BJT), il metallo non viene fuso durante la stampa; una parte “verde” viene creata utilizzando un legante che incolla la polvere metallica. Dopo la stampa, la parte deve essere sottoposta a sinterizzazione, come avviene nel CMF. Le parti prodotte con BJT tendono a essere meno dense e più fragili, quindi la fase di pulizia di questi componenti risulta essere molto più critica in presenza di dettagli e spessori sottili. Inoltre, il legante può ridurre la precisione e la sinterizzazione non sempre risulta uniforme. Sebbene la fase di stampa sia più veloce rispetto a PBF e CMF, il Binder Jetting richiede comunque una successiva fase di sinterizzazione, che può risultare lunga e complessa.
Rispetto ad altre tecniche di produzione del metallo più tradizionali, come lo stampaggio a iniezione di metallo (MIM) o la pressofusione, CMF offre invece una maggiore flessibilità progettuale e richiede investimenti iniziali decisamente più contenuti.
Perché dovresti considerare questa tecnologia
La tecnologia CMF è una vera rivoluzione nella produzione additiva di metalli e merita considerazione per una serie di motivi:
- Riduzione dei costi di produzione: CMF riduce i costi di macchinari e materiali poiché utilizza tecniche di stampa polimerica esistenti, come le Stampanti QLS di Nexa3D, disponibili a costi vantaggiosi e che quindi riducono l’investimento richiesto rispetto alle altre soluzioni per la stampa 3D di metalli.
- Efficienza energetica e impatto ambientale: CMF non richiede l’uso di potenti laser o sorgenti di calore concentrato per fondere direttamente il metallo e risulta quindi un processo meno energivoro. La possibilità di riutilizzare i materiali in eccesso porta anche a una riduzione complessiva dell’impatto ambientale.
- Flessibilità progettuale e velocità dei tempi di sviluppo: la tecnologia Cold Metal Fusion (CMF) non richiede supporti durante la stampa e questo contribuisce a ottimizzare l’intero ciclo produttivo. Inoltre, la resistenza delle parti “verdi” permette lavorazioni meccaniche preliminari, con un aumento della flessibilità progettuale.
Prima di procedere con l’acquisto di una stampante 3D, sia essa per lavorazioni in metallo o altri materiali, è sempre fondamentale valutare attentamente le necessità specifiche della tua azienda e i processi produttivi in cui verrà integrata.
Il nostro team di consulenti esperti in additive manufacturing è a tua disposizione per fornirti una consulenza su misura e aiutarti a individuare la soluzione più adatta per il tuo business. Inoltre, dopo l’acquisto della stampante 3D, ti accompagneremo nell’avvio e nell’uso corretto della macchina, garantendoti il massimo supporto.